[ad_1]
ABL Space Systems has been quiet since the company conducted its first launch attempt in January, which resulted in the rocket crashing back down to Earth a little over 10 seconds after lift-off. Now we know why: they have been very, very, very busy.
In a detailed blog post on Wednesday, CEO Harry O’Hanley described in detail the investigation the company conducted after the launch failure and the major upgrades it introduced to the RS1 rocket and GS0 ground system as it nears another launch attempt.
ABL is developing two systems: the lightweight, 87-foot-tall RS1 launch vehicle and a ground system called GS0, which O’Hanley referred to as “a launch site in a box.” Together, the two systems are meant to fulfill the dream of having a mobile, flexible all-in-one orbital launch system that can travel by shipping container to any site and be ready for launch a short time later.
“Imagine this: a convoy of container trucks arrive at a parking lot,” O’Hanley wrote. “A few days later, it’s an orbital launch site. That’s RS1 and GS0.”
The first launch ended shortly after lift-off due to a fire on the aft end of the first stage, which burned through critical electrical wires and shut down power, O’Hanley wrote. This led to the engines shutting off and the vehicle smashing into the ground. He said that the experience was difficult – but clarifying.
“All modern new launch vehicles from new companies have failed on their first flight. Even still, the outcome hurt,” O’Hanley wrote. “But it was a powerful tool. Failure forces everyone to reaffirm their conviction. It filters out those that don’t and drives hunger into those that do.”
ABL immediately got to work, launching an internal investigation the next day and quickly assembling a 10-person external independent review board. While there is not 100 percent certainty on the root cause of the fire, the company’s leading theory relates to the compact launch mount that forms the core of GS0. It was designed to fit into a shipping container, but that compactness positioned the rocket too close to the ground. Such close proximity “restricted the flow of engine exhaust gas” and drove up temperatures and pressures to exceed what the RS1 heat shield was designed to withstand, O’Hanley wrote.
The company has since made a number of upgrades to the rocket and ground system – some in response to the investigation, some that had already been in the works. One major change is the launch mount, which ABL completely redesigned to make it taller, wider, and with a larger exhaust area to prevent the engine exhaust gas from recirculating. The larger size means that the GS0 mount will transport in three pieces that can bolt together, instead of shipping in a single container. The image below shows the launch mount before and after the upgrades.
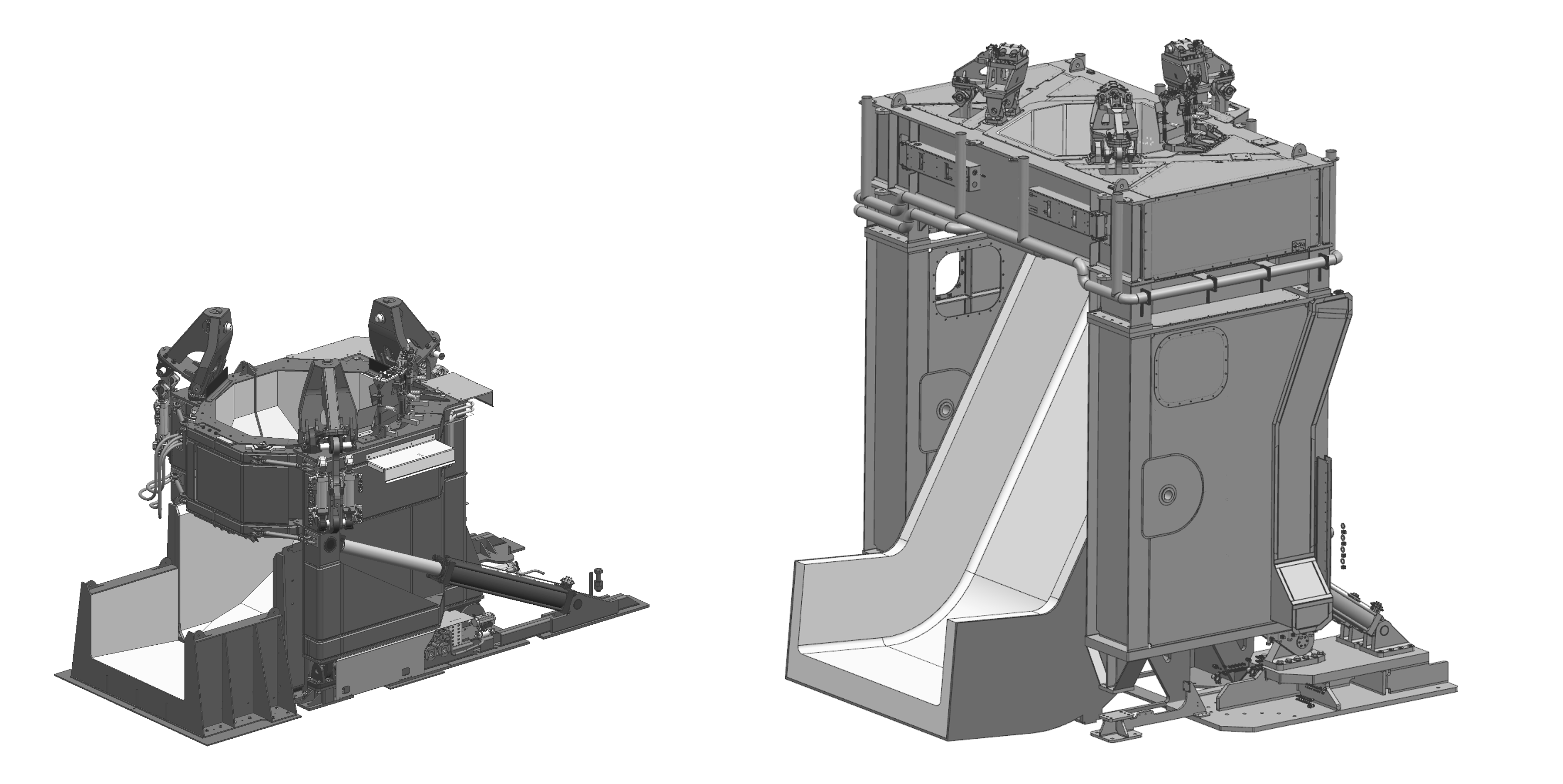
Image Credits: Harry O’Hanley (opens in a new window)
On the launch vehicle side, the company decided to move directly to an upgraded version of RS1 called Block 2, instead of flying a second Block 1 vehicle that was already built. Block 2 uses upgraded engines, and has other upgrades to the stage design, that will result in improved thrust and greater manufacturability, O’Hanley said.
“This strategy added significant design scope to the Flight 2 roadmap,” O’Hanley explained. “However, moving straight to Block 2 is a more direct path to building flight heritage on the configuration that will carry customer payloads to orbit.”
The company recently completed an operation called “Dock Dress,” one of the final activities in California before the system to Alaska for launch. After the system is sent to Kodiak, Alaska, the company will complete a few more milestone tests before launch, though O’Hanley did not specify a timeline for when that might take place.
“It was not in our plans to have RS1 grounded for most of 2023,” he wrote. “Our efforts this year were far away from the pad lights.”
[ad_2]
techcrunch.com